Partner
Mechanical design: printing metal parts thanks to 3D Precision SA
20 July 2021
Onboard the SP80 boat, there is no room for the irrelevant. Each part is carefully studied and optimised to fulfill the task for which it was designed.
With the support of our engineers, EPFL students focused on reducing the size and weight of the mechanical systems as much as possible, while guaranteeing the structural integrity of the parts. Here is the story of several months of work, during which the Swiss company 3D Precision SA played a key role!
From initial design to topological optimisation
The mechanical systems implemented in the boat are an important – but often hidden – part of the development. Yet it is still an exciting part!
First step: designing the necessary systems for the steering of the boat and for the kite. Then comes the whole process of optimizing the shape and weight of the various parts, while ensuring that they will not be damaged by the forces occurring during the navigation. Two students, Gabriel Bessette and Augustin Million, thus conducted topological optimisations (i.e. numerical simulations) to reduce the weight and size of the parts as much as possible while guaranteeing their mechanical resistance to the constraints they will encounter. As a result, instead of raw, solid, titanium parts, the parts are more organic, with a strengthened structure.
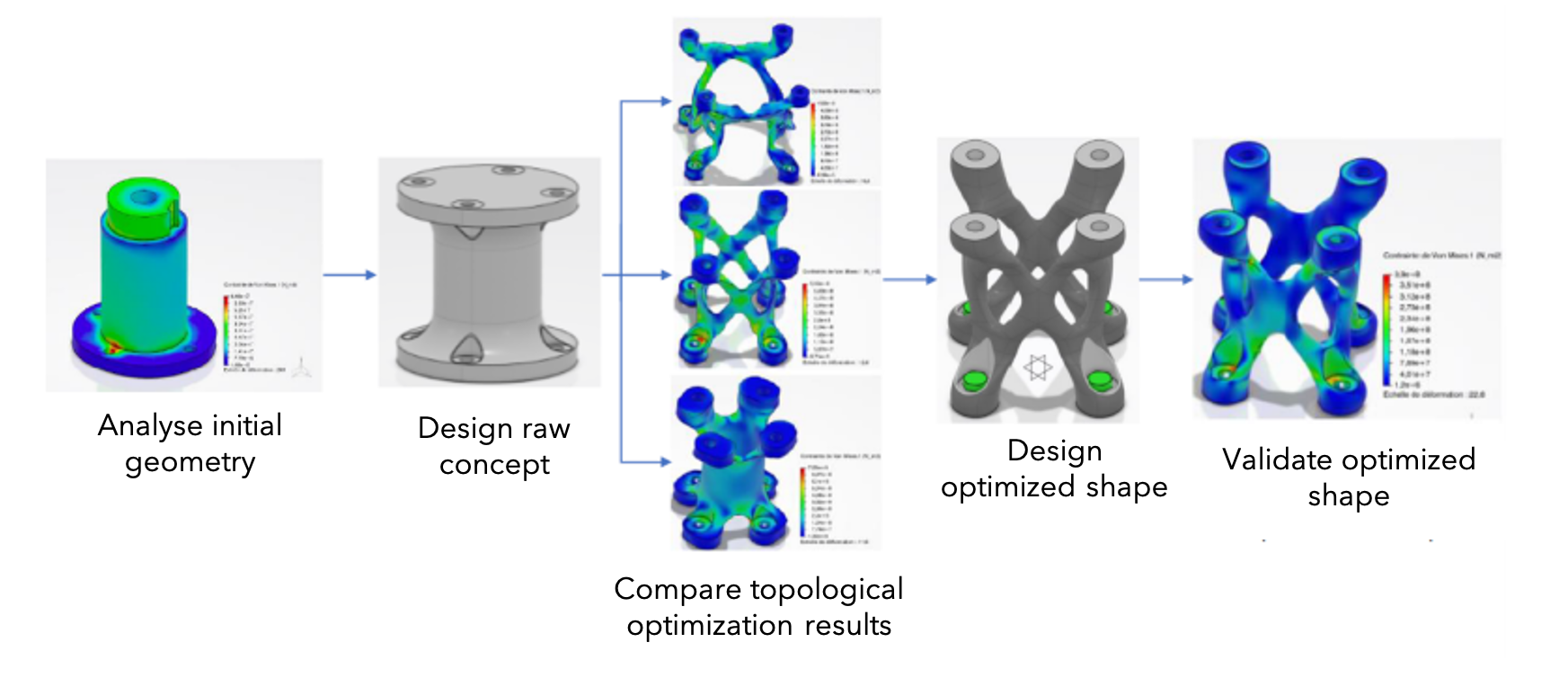
As an example, for the bearing housing for the rudder axis, the weight of the optimised part is 420g compared to 450g for the raw part. While the weight difference may not seem impressive, the optimised part is much more resistant to the same load. The stresses in the optimised version are only 145 MPa, whereas the original part generates stresses of up to 1100 MPa. Due to their more complicated shapes, these parts cannot be built in the traditional way, and this is where 3D Precision SA provides valuable support.
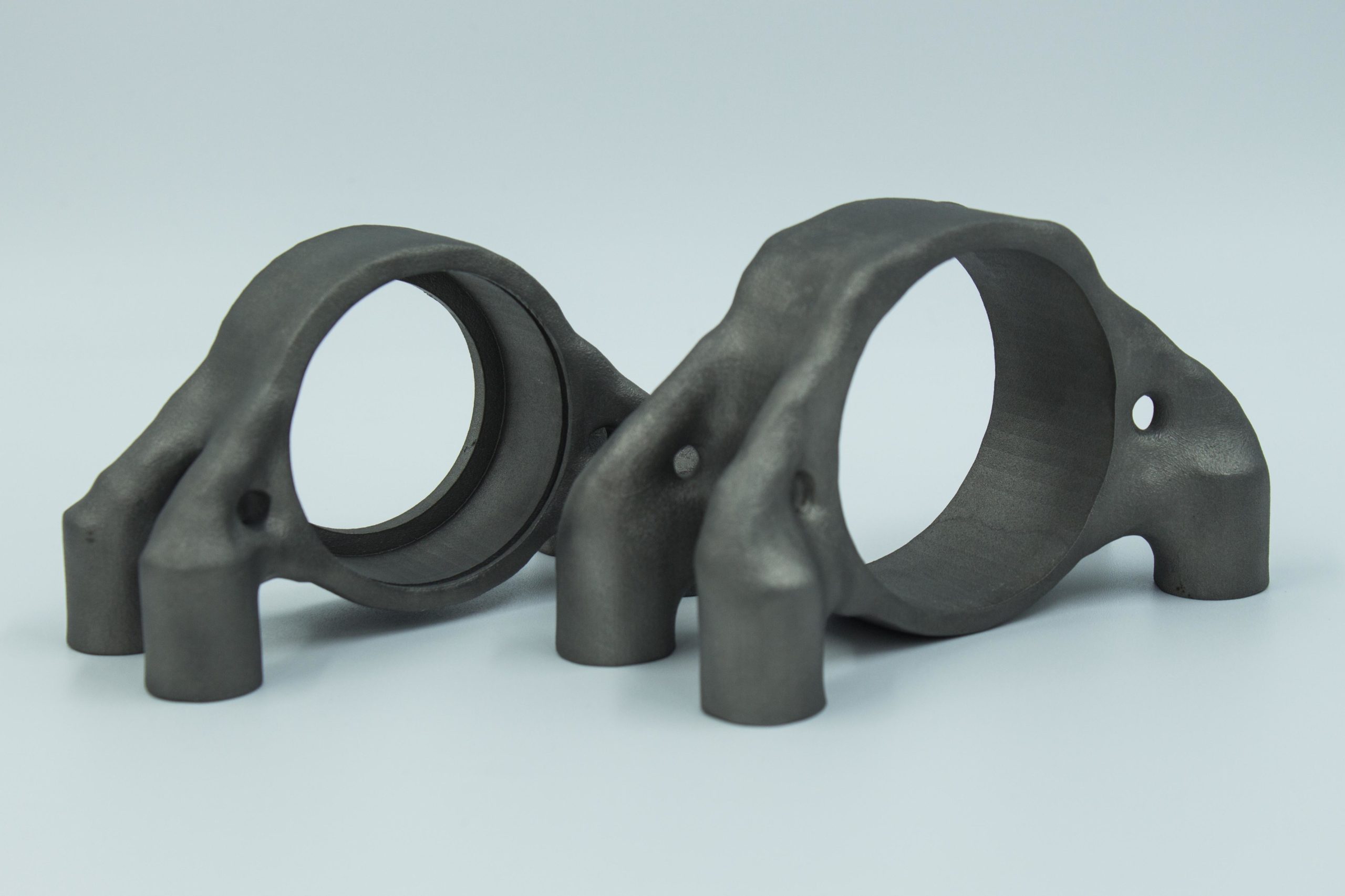
3D metal printing: an innovative solution
An innovative boat needs an innovative solution! From the beginning of the adventure, 3D Precision SA approached SP80, certain that the company could provide its expertise and support in metallic 3D printing. Adapted to complex geometries, from individual parts to medium-sized series, metallic 3D printing is undeniably THE solution for the SP80 project.
This additive production method is based on the selective laser fusion technique. Unlike conventional machining, which starts with a block of raw metal machined by a milling cutter, metal 3D printing uses a very high-powered laser to locally and progressively fuse a metal powder. In our case, we are using titanium powder, but other materials can be used to make parts in aluminium, steel, copper, etc.
This partnership really took shape with the manufacture of the first optimised mechanical parts. Before being implemented on the boat, their resistance had to be validated, a step that took place in the EPFL laboratories.
Validated mechanical parts ready for implementation
Now comes the most gratifying and visual stage: testing the resistance of the parts! Florentin Fellay, a student at EPFL and member of the SP80 association, has been working hard to prepare for these tests during the autumn semester of 2020. At the beginning of 2021, he was able to use a traction machine to characterise the strength of the bearing housing, going so far as to completely break the part.
Overall, the assembly meets the required specification ! Indeed, designed to break at a force of 72 kN (7 T), the first cracks were finally seen when applying a force of 91.6 kN (9 T).
We can therefore confidently implement these 3D printed titanium mechanical parts on the final boat. About fifteen parts will be made this way with the help of 3D Precision SA, bringing us a little closer to our attempt at a world sailing speed record in 2022.
If you are interested in the subject, you can watch the video Meet our partners | 3D Precision SA
Copyright 2025 | SP80 | All Rights Reserved