Partners
Optimization of ventilated hydrofoils thanks to ANSYS Fluent, CADFEM and artificial intelligence
February 2nd, 2021
SP80 aims to reach 80 knots (93 mph) and thus break the World Sailing Speed Record, only powered by the wind. To achieve this goal, the usual sailing codes have to be rethought, especially the hydrodynamic part of the appendages. In order to get the best out of the submerged profiles, the SP80 team has implemented an optimization approach based on cavitation tunnel tests coupled with numerical simulations carried out on ANSYS Fluent, all powered by artificial intelligence thanks to Neural Concept. Throughout the process, CADFEM advised the students and engineers in charge of these simulations, at the heart of the record quest.
Ventilation: an under-exploited phenomenon
Conventional drop-shaped hydrodynamic profiles tend to cavitate at around 50 knots (58 mph): at these speeds, the pressure drop is so important that the water starts to boil on the top surface of the profile. These vapor bubbles cause instability, drag and vibration, which can slow down the acceleration to 93 mph. To get around this problem, other types of profiles were designed in the 1950s mainly for military applications: ventilating profiles. With a triangular shape, this type of profile allows air from the atmosphere to dive into the extrados side caught by the depression, thus forming a large stable air bubble that will prevent cavitation inception: the profile ventilates. Although the performance at low speeds is not as good as that of a conventional profile, it has the advantage of allowing easy and stable acceleration up to 93 mph. Once the Cold War era was over, research into this type of profile became less frequent, hence the need for SP80 to determine internally the optimum profile shape for the record.

Validate the concept empirically through kitesurfing tests
In order to ensure that these ventilating profiles were an interesting solution for the World Sailing Speed Record, the co-founders of SP80 carried out numerous kitesurfing tests, testing more than 30 different profiles in the space of a few months. These tests allowed them to empirically validate the potential of such a solution. Benoit Gaudiot, kitesurfer, co-founder and pilot of the boat says: “I had a real feeling of stability at high speed. We reached more than 40 knots (46 mph) easily and without struggling to accelerate or stay on the board. We knew then that there was something to dig on that side”.
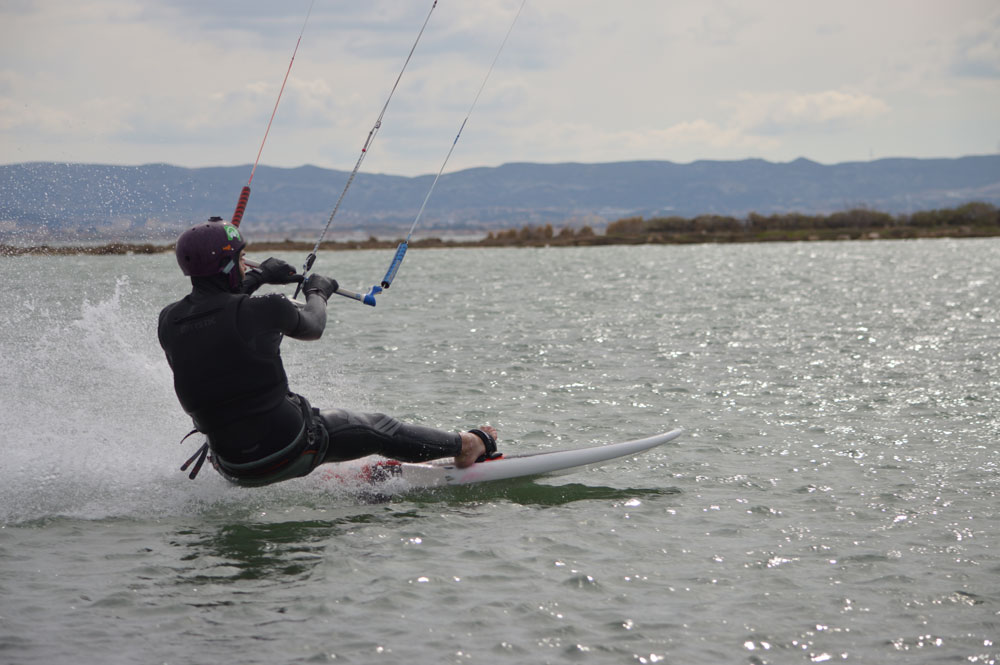
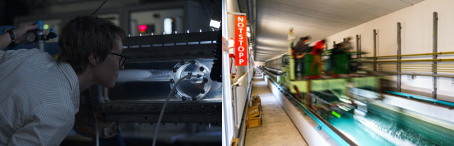
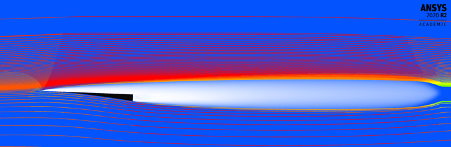
Essential dialogue between experimentation and simulation
Fortified by this experience, the research could then begin! It was essential for the team to combine numerical and experimental tests in order to ensure that the results on these still little-used profiles were consistent. Tests were thus carried out in 2D in the cavitation tunnel of the Laboratory of Hydraulic Machines (LMH) at EPFL, then in 3D at the HEPIA hull basin, then at METAS.
At the same time, a numerical set-up was created on ANSYS Fluent. Here too, studies began in 2D, in order to considerably simplify the problem while remaining faithful to the observations made in the cavitation tunnel. Working in 2D made it possible to avoid modelling the free surface, which can be very complex. The team was then able to quickly refine all the solver parameters before transposing these settings to a 3D model. After multiple tests and with CADFEM’s valuable advice, the “Volume of Fluid” model, the most common for this type of application, proved to be the most effective for modelling the presence of the two air-water phases. Turbulence, on the other hand, is modelled with the k-omega SST model.
Artificial intelligence at the service of optimization
Once the right parameters had been identified, the hydrodynamics team was able to exploit all the power and robustness of the ANSYS Fluent software: more than 500 simulations were generated in record time! The results obtained were used to feed a neural network, SP80 having chosen to use artificial intelligence to optimize these profiles. Thanks to the EPFL start-up Neural Concept, it was possible to predict the performance of any form of foil from the results obtained on ANSYS Fluent. It was therefore possible to virtually test a very large number of designs and the optimization algorithm developed made it possible to explore shapes that the team might not have thought of with a “conventional” iterative approach.
The profile thus obtained could therefore be built and then tested in the LMH’s cavitation tunnel to validate its characteristics and confirm a performance gain of almost 20%, which immediately translates in reality into several mph more speed!
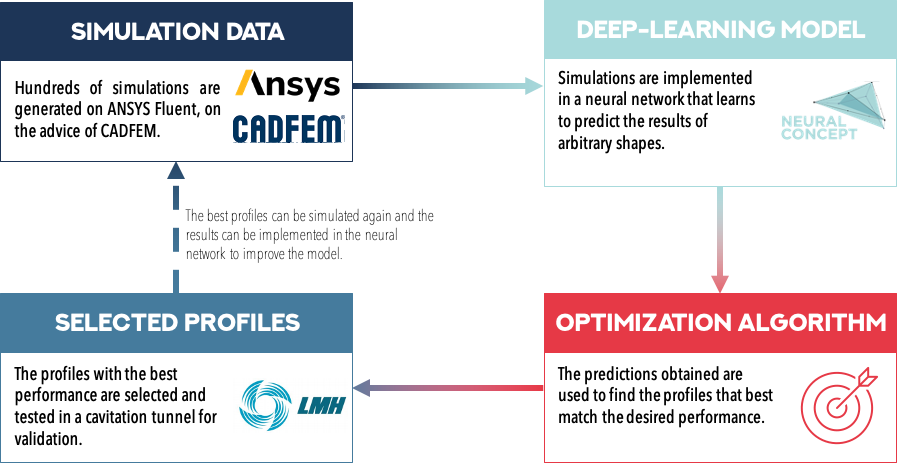
CADFEM, a valuable support in setting up simulations
The numerical simulations carried out on ANSYS Fluent were at the heart of the SP80 hydrofoil optimization process and the capabilities offered by the software have resulted in time and precision savings, essential for breaking the world sailing speed record in 2022. In order to make the best use of all the software’s resources, the SP80 hydrodynamics team, composed entirely of EPFL students, was able to count on CADFEM’s invaluable advice, in particular that of Demian Lauper and Christopher Blomberg. Their support helped to improve the simulations carried out on ANSYS Fluent and at the same time allowed the students to perfect their knowledge of the software.
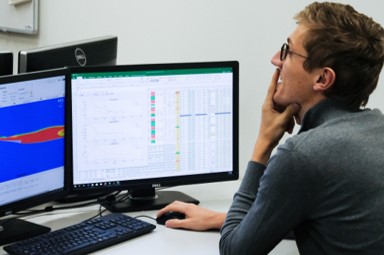
Aurore Kerr, communication manager
Copyright 2025 | SP80 | All Rights Reserved