Projet
La construction de notre modèle réduit: le précieux soutien de nos partenaires pendant la pandémie de la COVID-19
14 Septembre 2020
Comment construire un prototype quand le monde est à l’arrêt et que chacun doit rester chez soi? A l’heure des premières mesures de confinement en mars 2020, personne chez SP80 n’avait vraiment de réponse à cette question. Cependant, grâce à la motivation et à la volonté des étudiants et ingénieurs impliqués, ainsi qu’au soutien sans faille de nos partenaires, nous sommes fiers d’annoncer aujourd’hui que le modèle réduit a bien touché l’eau et enchaîne depuis plusieurs semaines les tests d’optimisation. Retour sur ces derniers mois cruciaux pour SP80!
Le confinement ou la nécessité de se réorganiser
En mars dernier, alors que l’équipe en charge de la construction du prototype venait de s’agrandir profitant du début du semestre académique, la crise sanitaire entraîne la fermeture du site de l’EPFL et de ce fait l’impossibilité pour l’équipe de commencer la construction du modèle réduit du bateau.
Mais chez SP80, l’étonnement et la stupeur laissent alors vite place à la réorganisation: “Il a fallu revoir le planning initial qui alternait développement et construction des différents éléments. Nous n’avions plus accès aux ateliers, nous nous sommes donc concentrés sur la finalisation des designs et la préparation des protocoles de construction en échangeant toutes les semaines par visioconférence ou par messages. Il fallait être prêt à reprendre la construction dès que les conditions le permetteraient pour retarder au minimum la mise à l’eau et les 1ers tests”, explique Romain, ingénieur responsable de la réalisation du prototype.
Le travail à distance se met rapidement en place, grâce notamment au partenariat avec Dassault Systèmes par le biais de la 3DS Academy. Blaise Ribon, étudiant en 3ème année de Bachelor de Génie Mécanique témoigne: “L’accès aux licences étudiantes 3DExperience nous a permis de peaufiner les derniers détails des pièces à construire et ce de manière collaborative avec les différents étudiants impliqués, tout en étant installé chez nous. Sans ces accès, nous aurions sans doute laissé beaucoup plus de temps et d’énergie!”
Une remise en route lente mais efficace
En parallèle, l’équipe s’active pour trouver un local afin d’assurer la construction et l’assemblage du prototype dans de bonnes conditions. La Fondation INARTIS nous offre une solution idéale en nous mettant à disposition un espace de travail non loin de l’EPFL. La construction peut alors reprendre tout en respectant les règles sanitaires en vigueur.
Quelques semaines plus tard, avec l’assouplissement des mesures de confinement, certains collaborateurs de l’EPFL sont autorisés à revenir sur le campus. Le laboratoire du LPAC et le fablab du SKIL de l’EPFL sont alors d’un soutien précieux, en se coordonnant avec l’équipe pour réaliser les pièces que les étudiants ont pu concevoir depuis chez eux les mois passés.
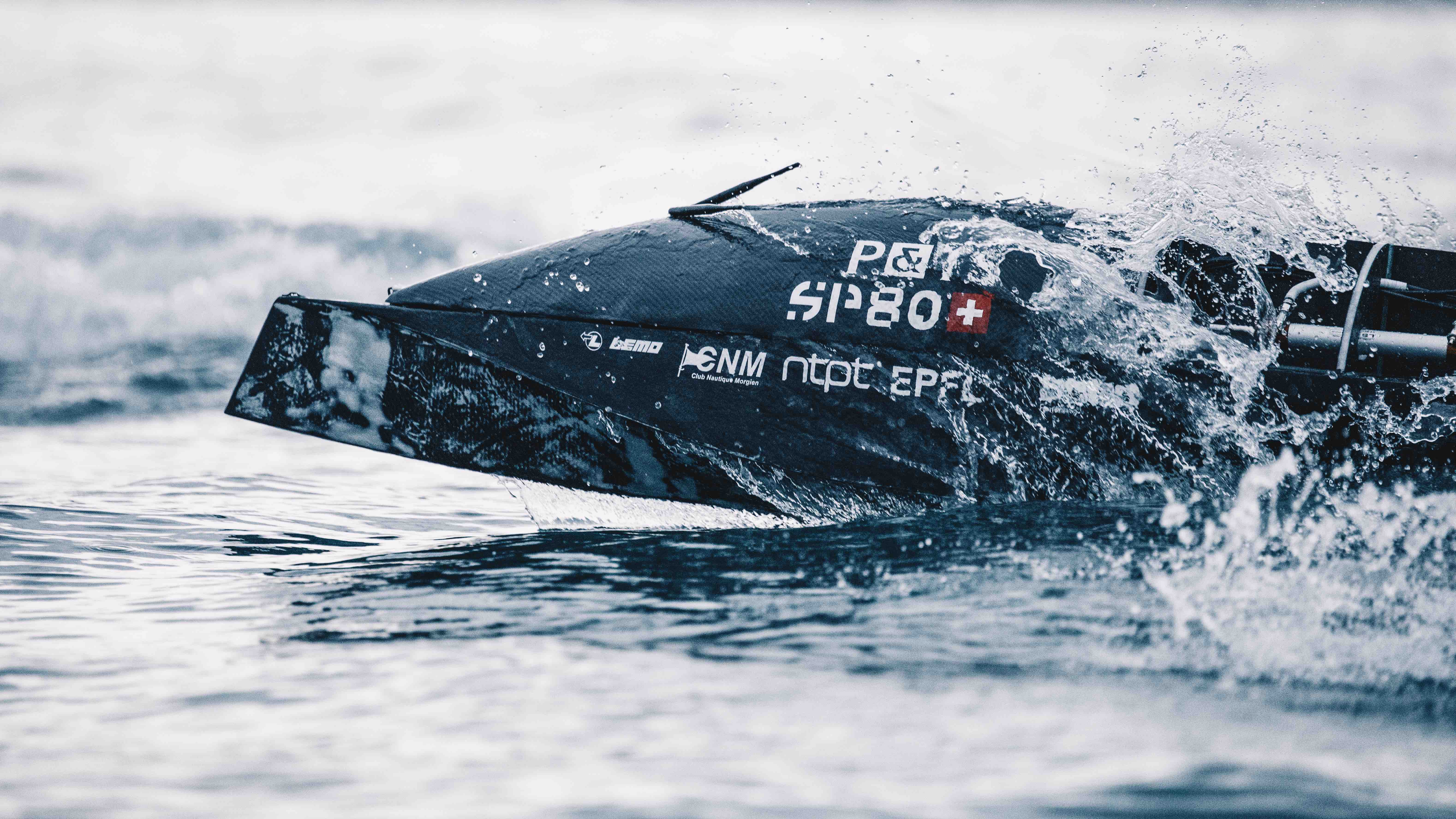
Au mois de juin, le rythme devient plus soutenu, le planning se remplit et de nouvelles pièces sont produites tous les 3 jours, grâce notamment à la réactivité de Swiss Composites. Océane Suchel, étudiante en 3ème année de Bachelor en Génie Mécanique se souvient de cette période intense: “Quel soulagement de pouvoir enfin voir les avancées concrètes sur le prototype! Nous avions de l’énergie à revendre après ces 2 mois de confinement et la soif de mettre la main à la pâte. C’était l’occasion de passer de l’autre côté de l’écran et pouvoir enrichir notre bagage technique d’ingénieur en s’occupant de la production. Travailler avec de la fibre de carbone de chez NTPT était notamment quelque chose que je n’avais jamais abordé et nous avons pu tous apprendre et progresser au fur et à mesure des pièces produites.” Un safran, un foil puis deux flotteurs: le modèle réduit prend forme au fur et à mesure des semaines.
L’équipe en charge de l’électronique embarquée se met aussi au travail: “Il est primordial de collecter des données lors des tests pour comprendre le comportement du prototype et donc du futur bateau.” explique Benjamin Bonnal, ingénieur en charge des systèmes électroniques. “Les différents capteurs que nous avons prévus sont reliés grâce à des connecteurs étanches LEMO. Nous avions bien travaillé en amont sur les différents passages de câbles pour avoir des circuits clairs et simples. Après quelques heures de calibration à terre, l’ensemble de l’électronique était fonctionnel et prêt à collecter des données!”
La récompense: la mise à l’eau
Finalement, seulement quatre mois après le début du confinement, le prototype a touché l’eau au Club Nautique Morgien (CNM), partenaire technique pour la réalisation des tests. Une journée mémorable pour toute l’équipe qui se souvient des 1ers doutes face à l’inconnu de la situation générée par la pandémie: “Cette mise à l’eau est la concrétisation d’intenses mois de travail. Tout le monde était si fier d’avoir contribué à la réalisation de ce prototype que nous avons laissé exploser notre joie quand ce dernier a fait ses 1ers bords.” se souvient Tanguy Desjardin, étudiant de Bachelor en Génie Mécanique. Le challenge était de taille et l’équipe a su le relever, preuve de sa motivation, de sa passion et de sa cohésion. Mais cela n’aurait pas été possible sans nos partenaires qui ont continué de croire au projet même dans les périodes les plus difficiles. Il est certain que nous ressortons plus fort de cette aventure mais déjà tournés vers les prochaines étapes qui nous mèneront à battre le record du monde de vitesse à la voile en 2022.
Océane Suchel, membre de l’équipe de prototypage & Aurore Kerr, responsable communication
Photos: © Guillaume Fischer
Copyright 2025 | SP80 | Tous Droits Réservés