INFOGRAPHIC: HOW DO WE SHAPE OUR BOAT?
24 août 2021
After 40’000 hours of design, we are finally building our little rocket! The boat for the record is being manufactured at the renowned shipyard Persico Marine and the first tests on the water will take place in 2022… are you excited? We are too!
In the meantime, here are the main construction steps.
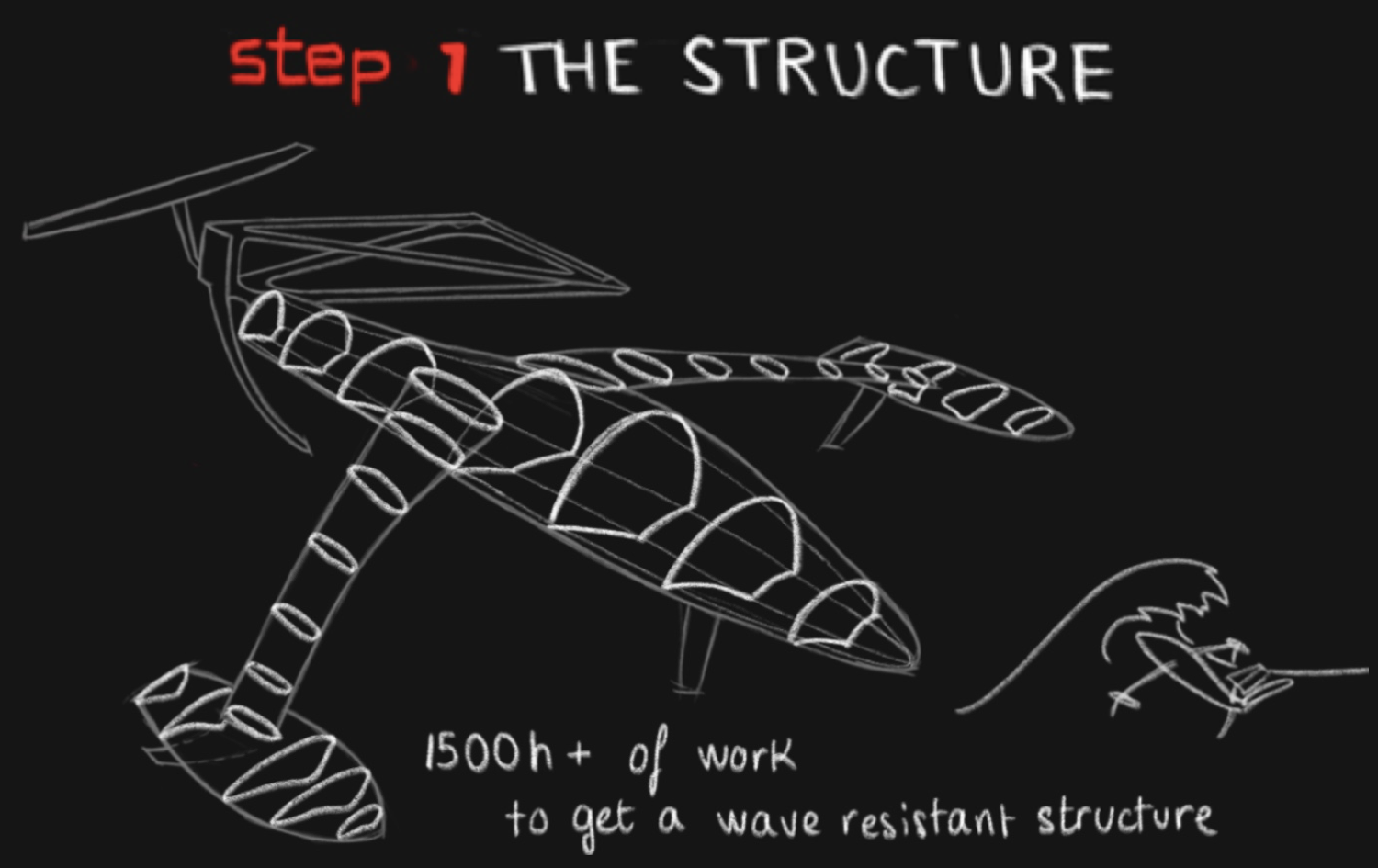
STEP 1 – the structure
Reaching 150km/h with a sailboat is a nice challenge.
But, at this speed, the stresses on the structure are much greater than at lower speeds.
We need to think about a structure that can withhold these stresses, whether they are due to wind, waves, or something else. For this, we had help from Collier Aerospace and Gsea Design.
All these computations took us more than 1500 hours of work!
Step 2 – carbon-made molds
Once the structure is approved, custom molds are made. During the curing process, each mold must react exactly the same way as the part inside it.
Our boat is 100% carbon-built, therefore we have to use molds of the same material so that we don’t have any surprises during the process!
14 carbon-made molds were made in Spain by our partner Synergia Racing Group.
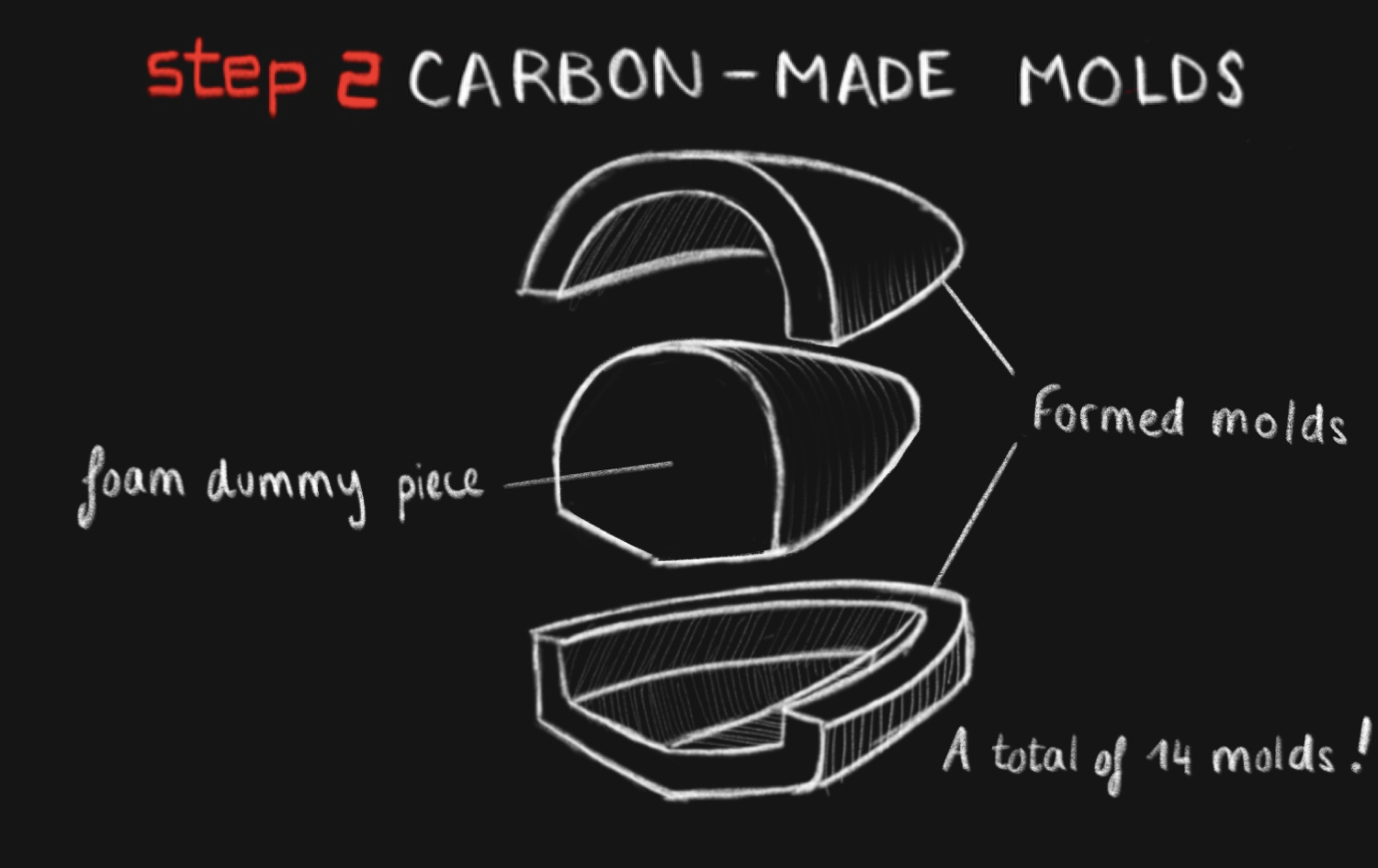
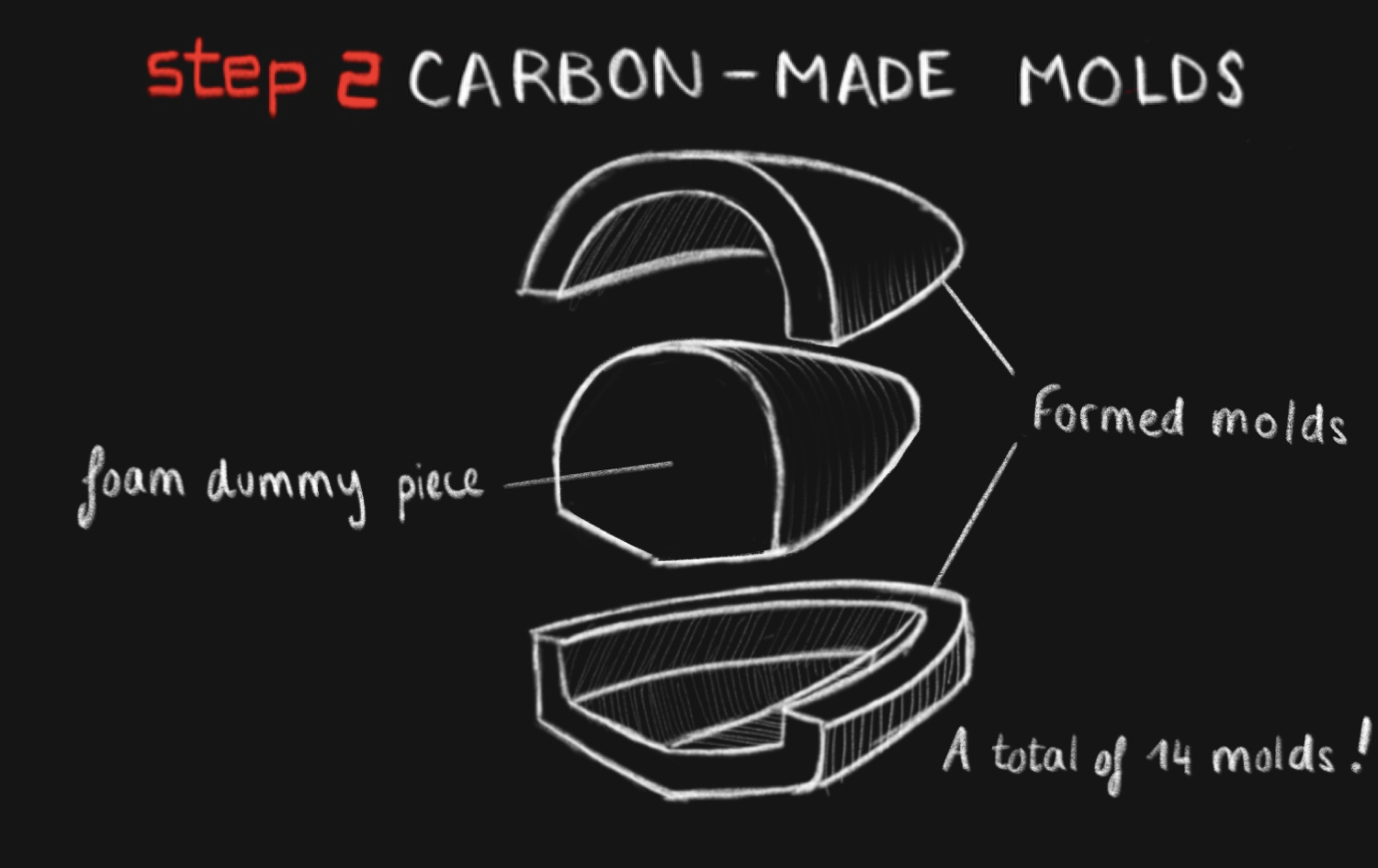
Step 2 – carbon-made molds
Once the structure is approved, custom molds are made. During the curing process, each mold must react exactly the same way as the part inside it.
Our boat is 100% carbon-built, therefore we have to use molds of the same material so that we don’t have any surprises during the process!
14 carbon-made molds were made in Spain by our partner Synergia Racing Group.
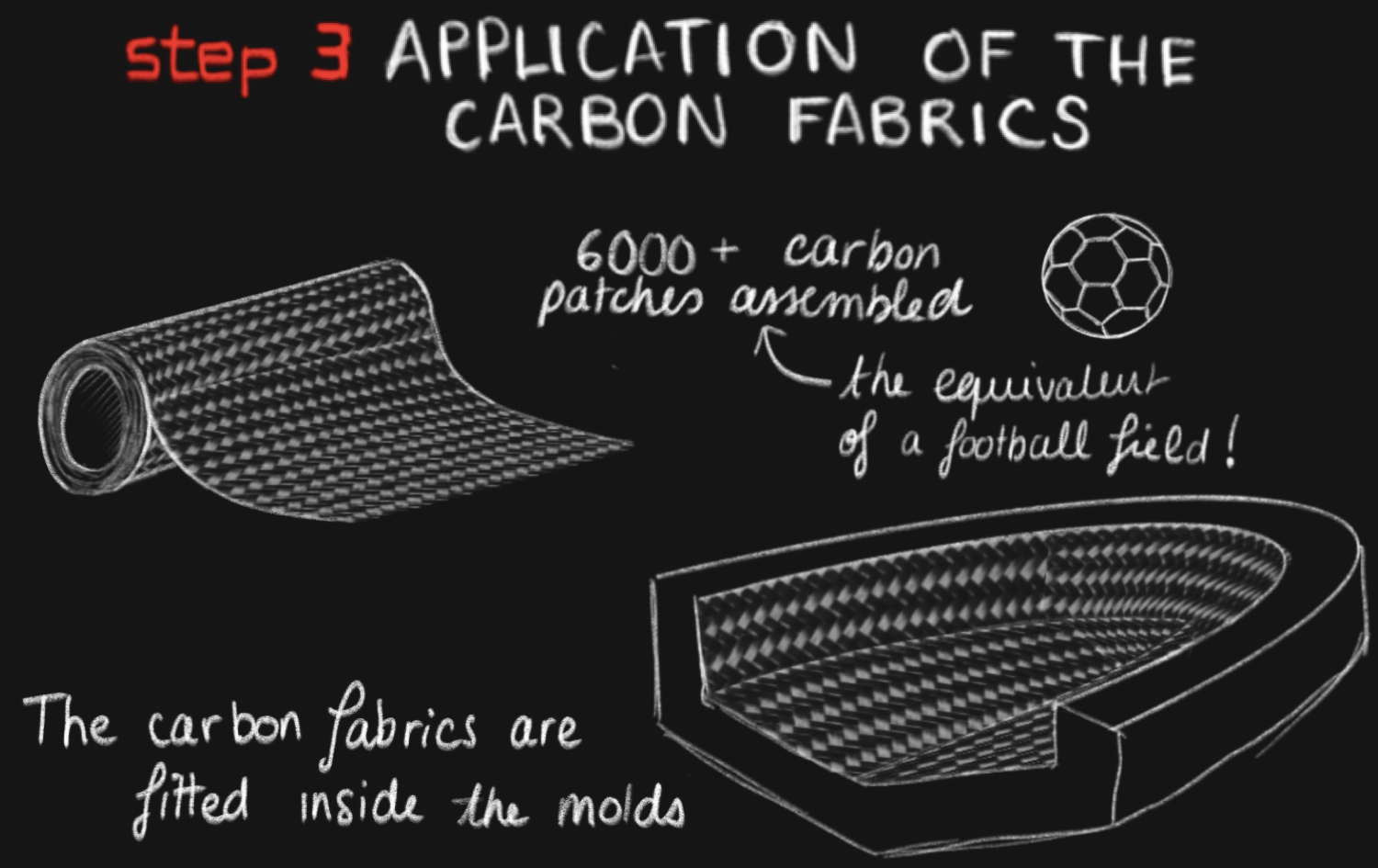
STEP 3 – APPLICATION OF THE CARBON FABRICS
Once we are finished with the molds, it’s time to apply thousands of carbon kits inside to create the parts!
We are mainly using TPT carbon, produced by our partner North Thin Ply Technology. It’s a very thin and strong material from the prepreg family that requires a lot of expertise to process.
This step is where the Italian shipyard Persico Marine is entering the game, using their long history of experience to expertly apply 6000+ carbon patches inside our molds. The area will be equivalent to a football field!
STEP 4 – CURING OF THE PARTS
The parts need to be cured! This giant furnace is called an autoclave and applies pressure equivalent to that of 70m underwater to each piece.
Why? Because the high pressure expels air from the material. The goal is to have the most compact pieces possible, to avoid small air bubbles which could cause cracks in our boat over time.
Each part is going to stay in the autoclave for 8 hours!
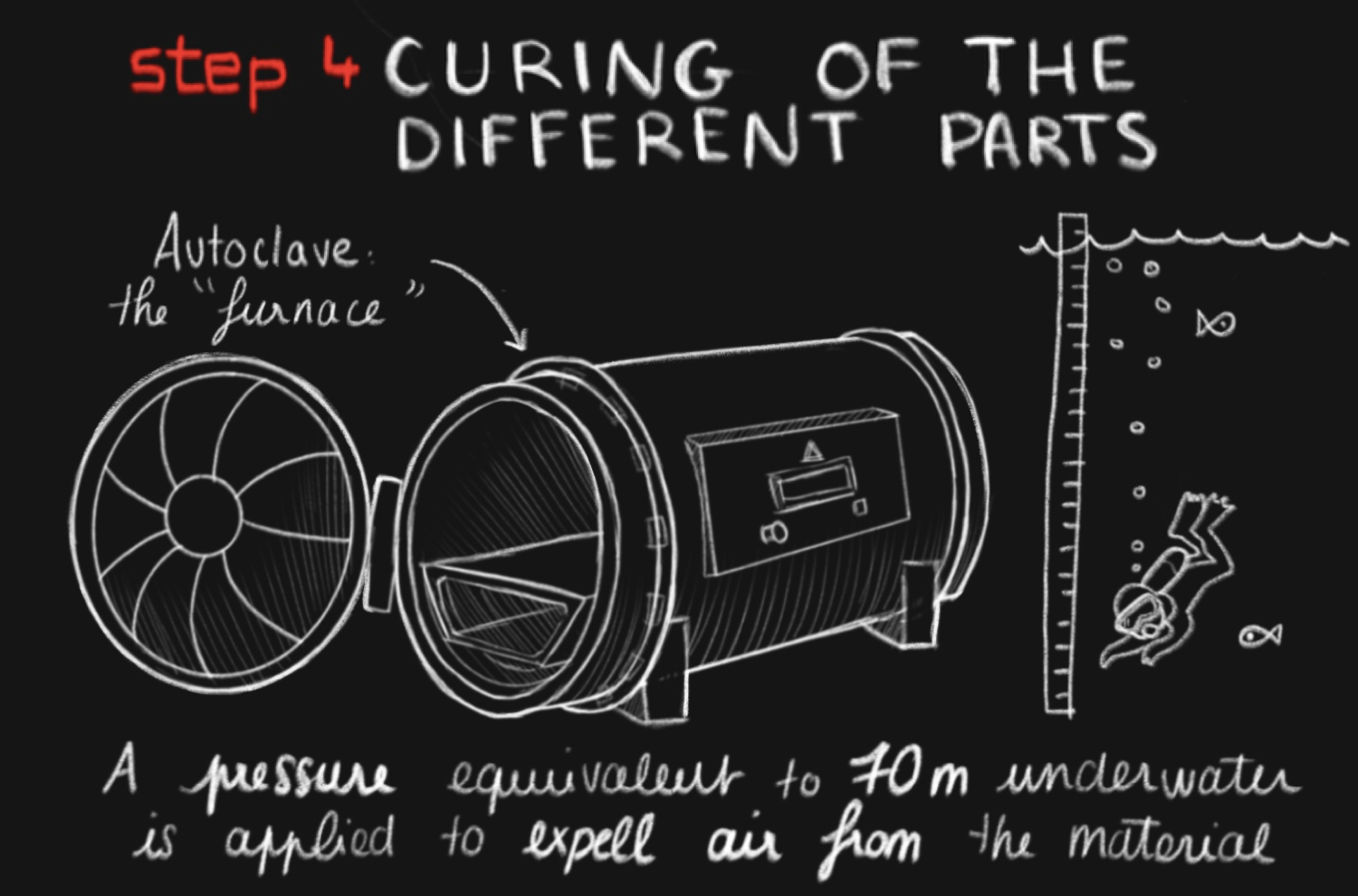
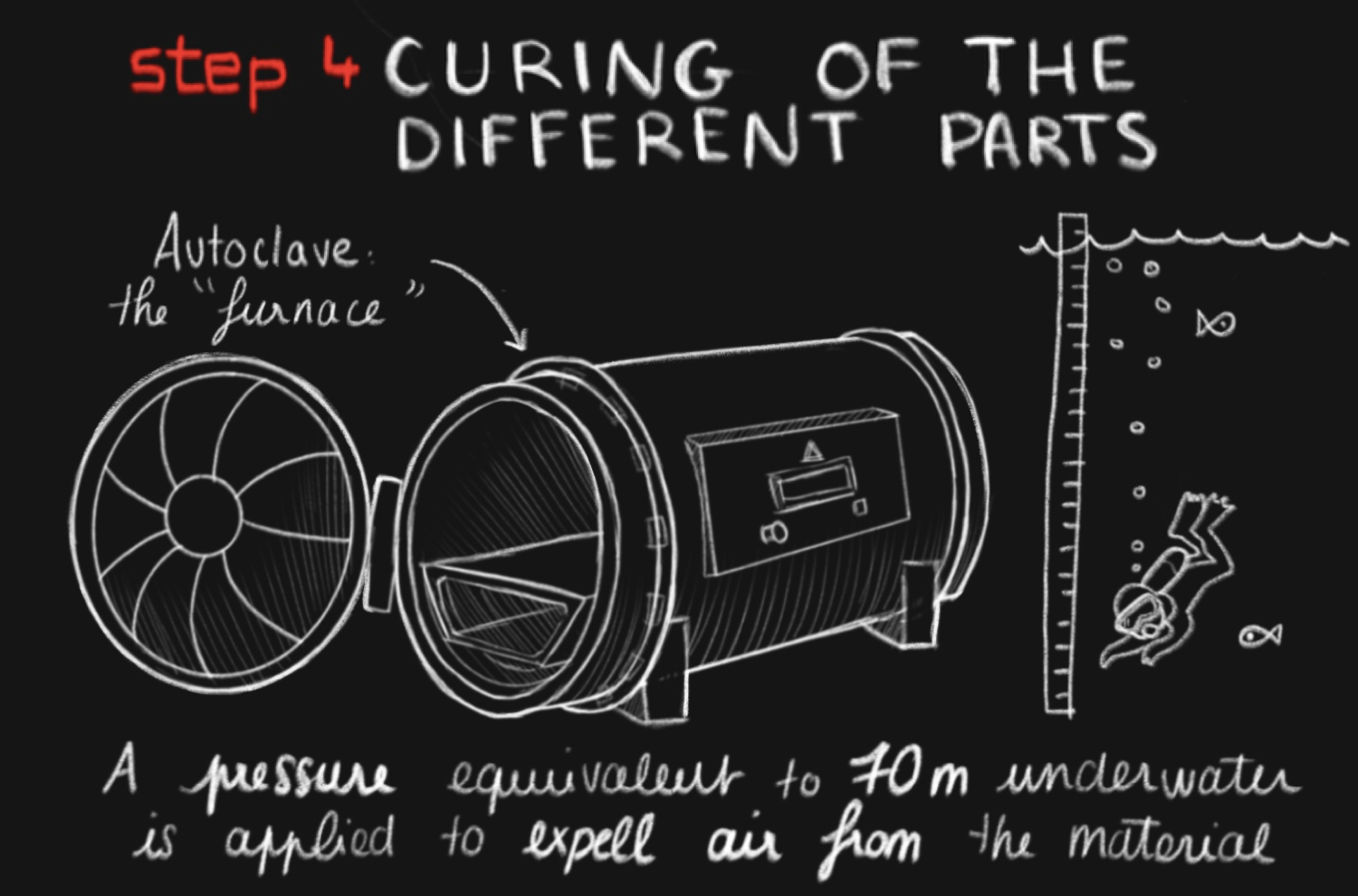
STEP 4 – Curing of the parts
The parts need to be cured! This giant furnace is called an autoclave and applies pressure equivalent to that of 70m underwater to each piece.
Why? Because the high pressure expels air from the material. The goal is to have the most compact pieces possible, to avoid small air bubbles which could cause cracks in our boat over time.
Each part is going to stay in the autoclave for 8 hours!
step 5 & 6 -assembling our boat and finishing touches
The 1500 parts are assembled and the boat is taking shape, the mechanical parts (steering wheels, pedals…) are added inside the cockpit and the hulls are painted with our colors… we “just” have to put the rocket in water and reach 150km/h.
To watch this part, let’s meet in 2022!
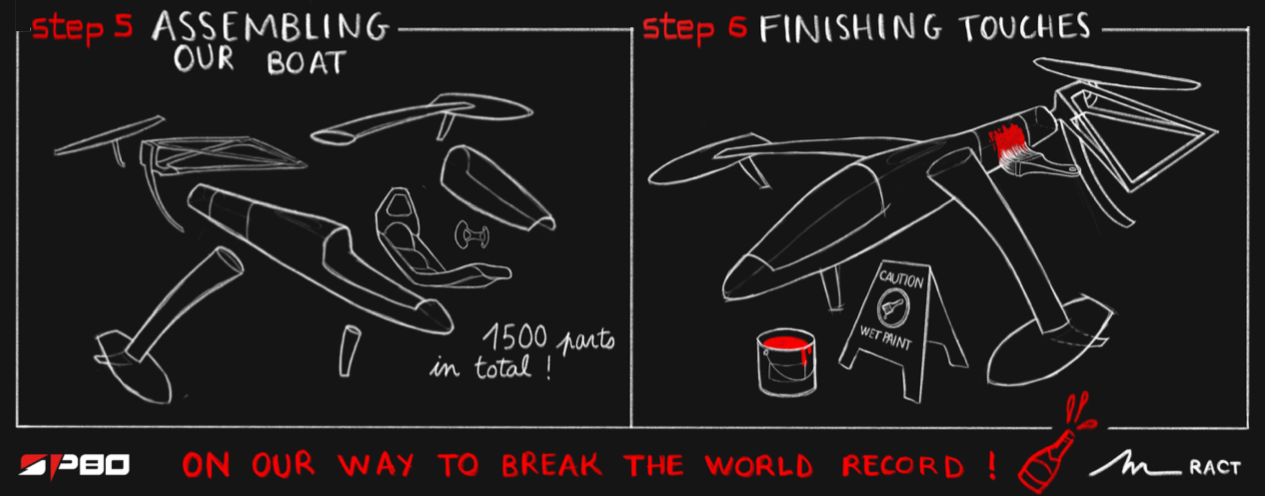
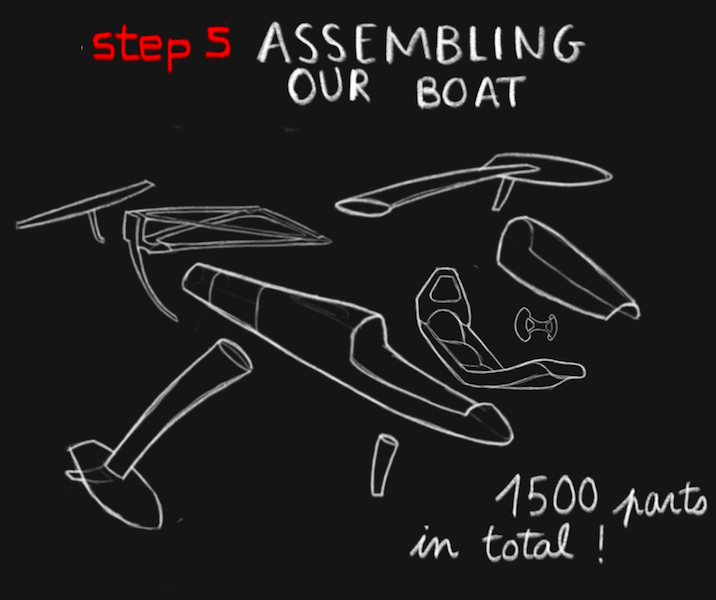
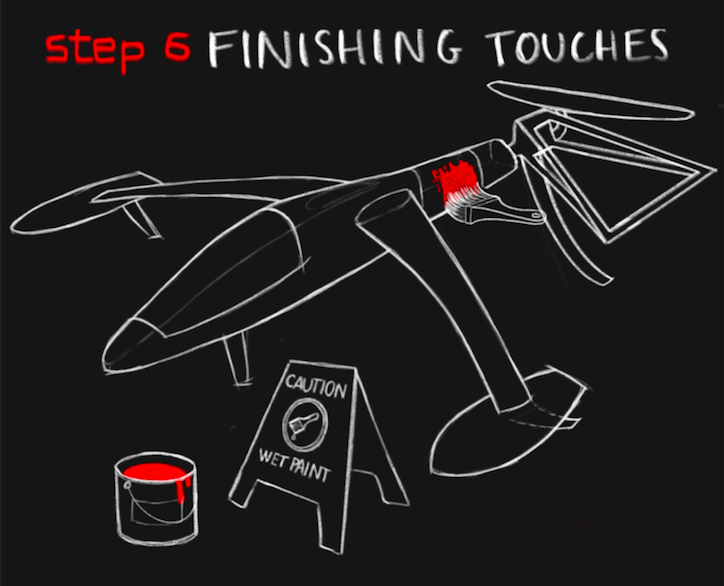
step 5 & 6 -assembling our boat and finishing touches
The 1500 parts are assembled and the boat is taking shape, the mechanical parts (steering wheels, pedals…) are added inside the cockpit and the hulls are painted with our colors… we “just” have to put the rocket in water and reach 150km/h.
To watch this part, let’s meet in 2022!
Copyright 2025 | SP80 | All Rights Reserved