Le processus de construction : des croquis au bateau final #4
25 février 2023
Construire un bateau en carbone capable de battre le record du monde de vitesse à la voile est le fruit d’une étroite collaboration entre SP80, North Thin Ply Technology, Persico Marine et Sinergia Racing Group. Ces quatre acteurs échangent tout au long du processus de construction, processus qui comprend de nombreuses étapes avant d’arriver au produit fini: notre bateau.
Dans cette série d’articles, nous décortiquons ces différentes étapes, de la création des moules à l’assemblage des pièces produites.
La lamination: donner vie aux pièces
Après avoir reçu notre kit de construction (voir article précédent), Persico Marine a tout en main pour commencer à déposer les plis dans les moules. Ils suivent les étapes décrites dans le plybook et déposent les plis les uns après les autres.
Entre chaque séquence (pour rappel, chaque couche de carbone), ils réalisent une mise sous vide. Cette étape permet de compacter les plis un maximum entre eux avant de cuire l’ensemble moule-pièce dans un four, appelé autoclave, qui applique une très forte pression sur la pièce pendant la cuisson. Ce four garantit un compactage parfait et donc l’absence de bulle d’air dans la pièce. Il est crucial d’éviter les bulles d’air : ces porosités créent des risques de fissure, qui peuvent potentiellement casser la pièce.
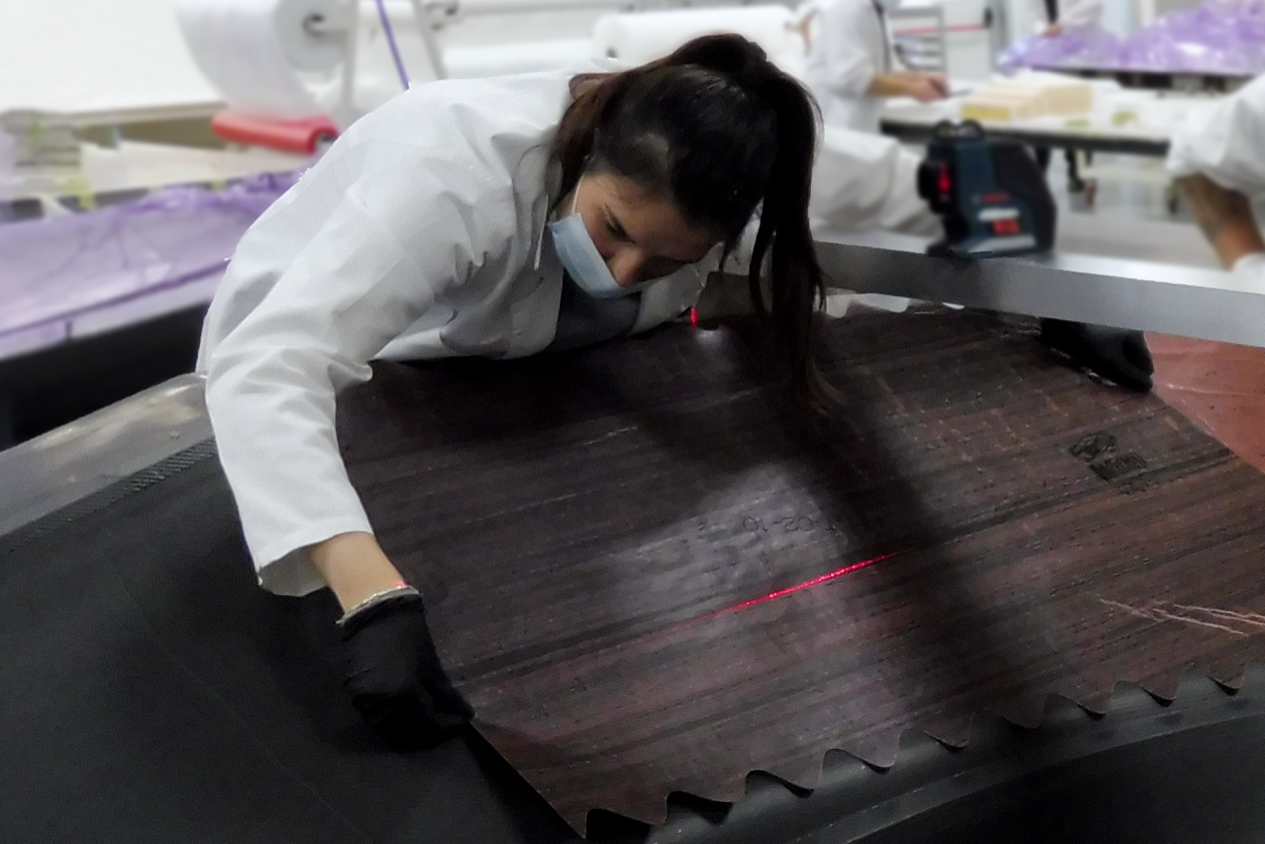
Pose d’une couche de carbone dans le moule : c’est la lamination !
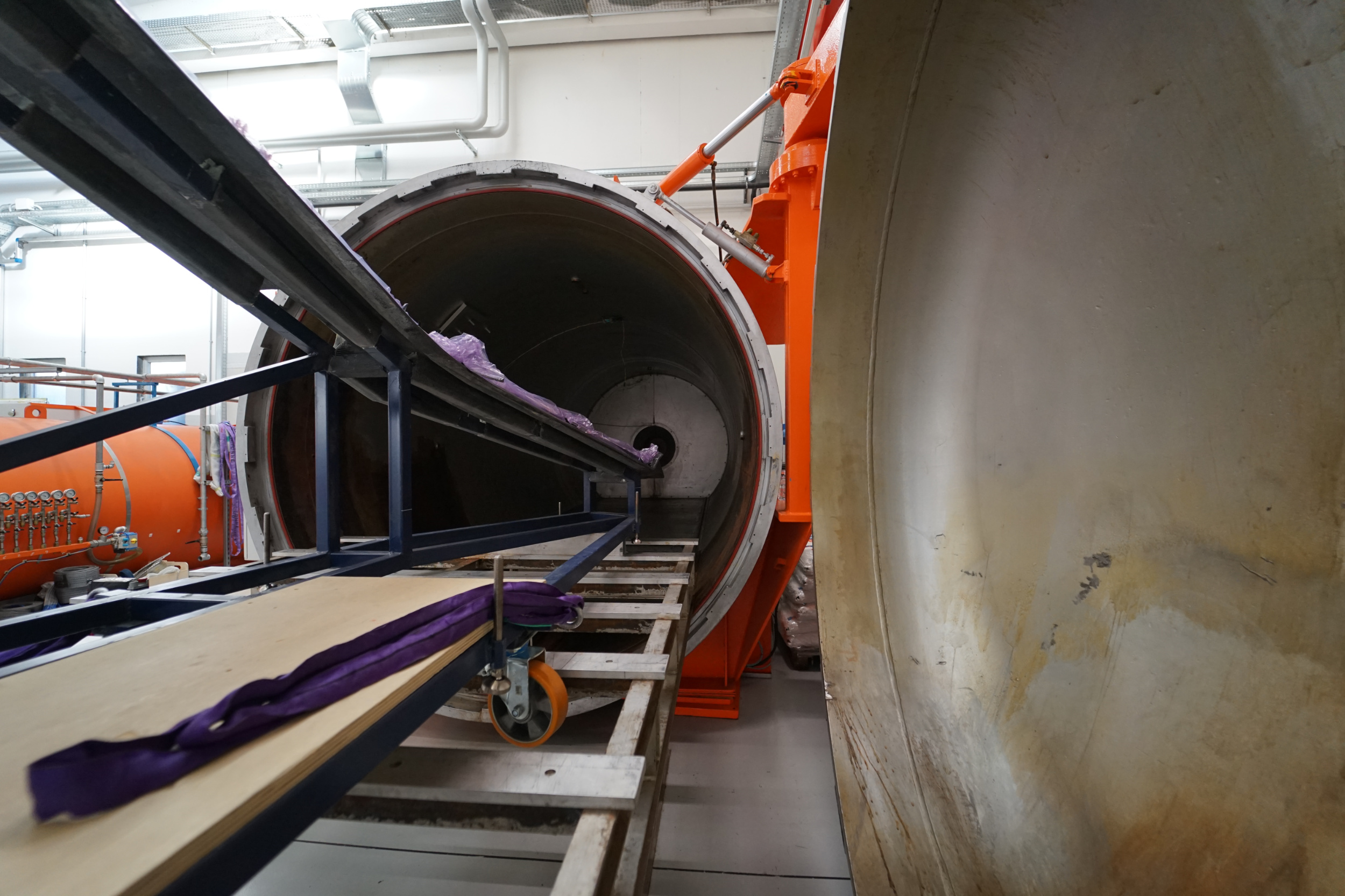
L’ensemble moule-pièce de notre bras de liaison qui sort de l’autoclave.
Une fois la première peau (peau extérieure) cuite dans l’autoclave, il faut placer les mousses utilisées dans les structures sandwich.
RAPPEL : STRUCTURE SANDWICH VS. MONOLITHIQUE
Une pièce peut-être constituée uniquement d’une seule peau de carbone (structure monolithique). A certains endroits de notre bateau, définis lors de l’analyse structurelle réalisée au préalable, nous utilisons cependant une structure sandwich : un matériau appelé « âme » (souvent de la mousse) est ajouté entre deux peaux de carbone afin d’avoir une meilleure rigidité de la pièce pour une masse équivalente.
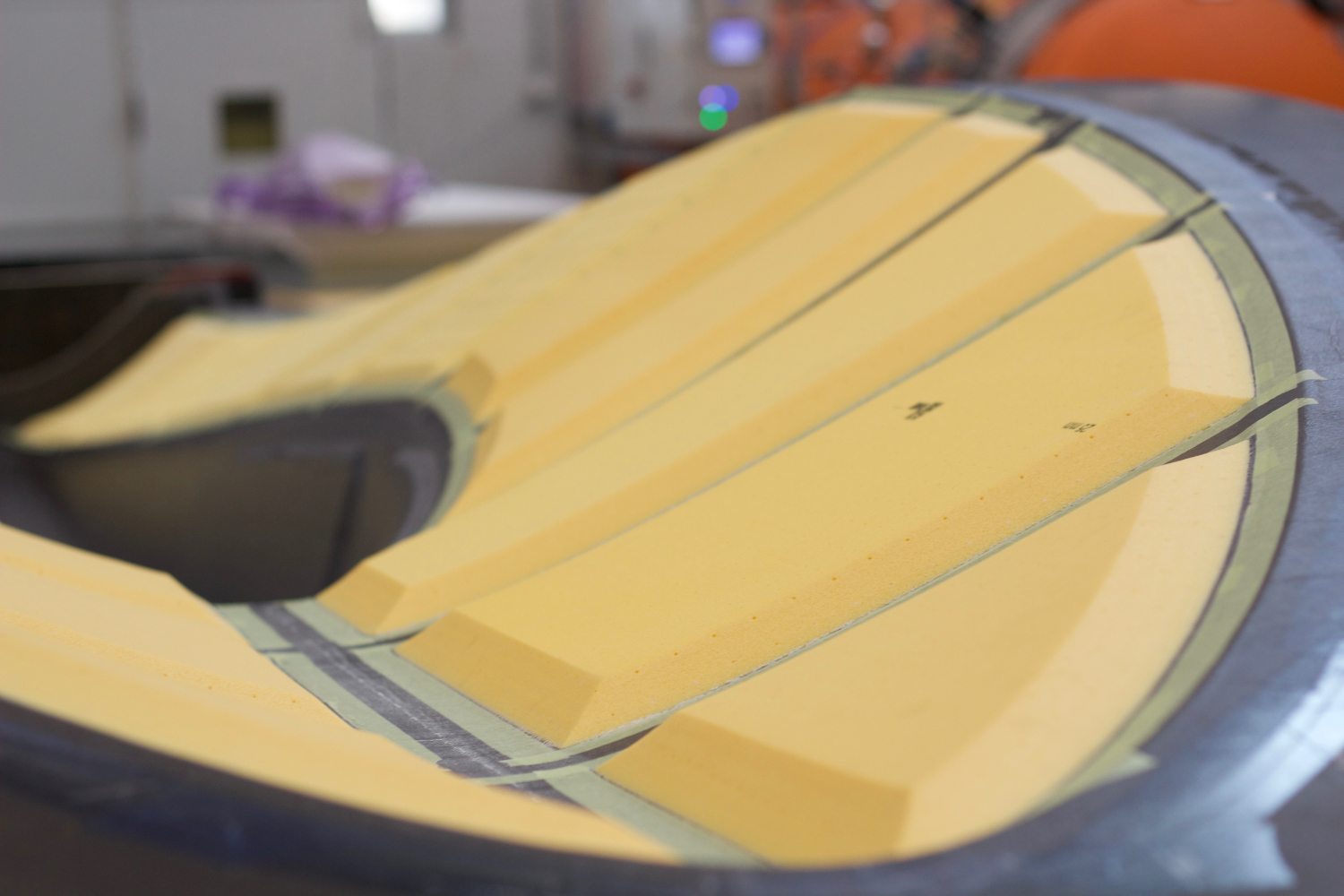
En jaune, la mousse posée lors de la construction de notre coque centrale.
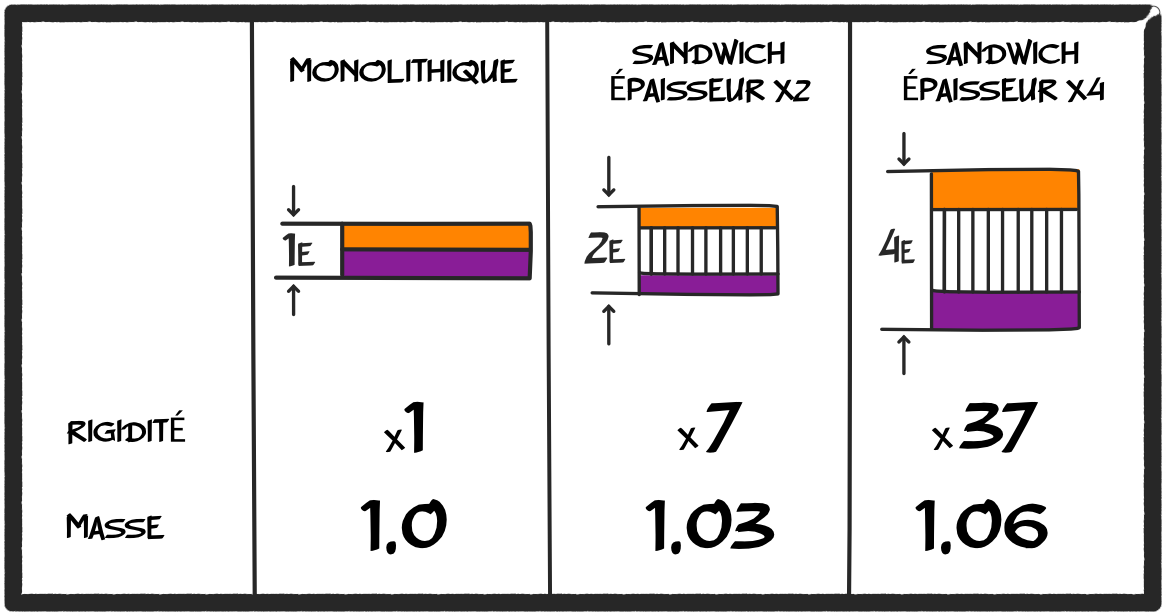
Une structure sandwich permet d’augmenter très facilement la rigidité d’une pièce !
Les mousses sont maintenues en place sur le carbone grâce à un film de colle. Le tout repart alors en cuisson pour que le film de colle durcisse et fige complètement le positionnement. Puis le chantier continue la lamination en déposant les plis de la peau intérieure de la pièce. Le schéma suivant reprend la séquence complète de la lamination :
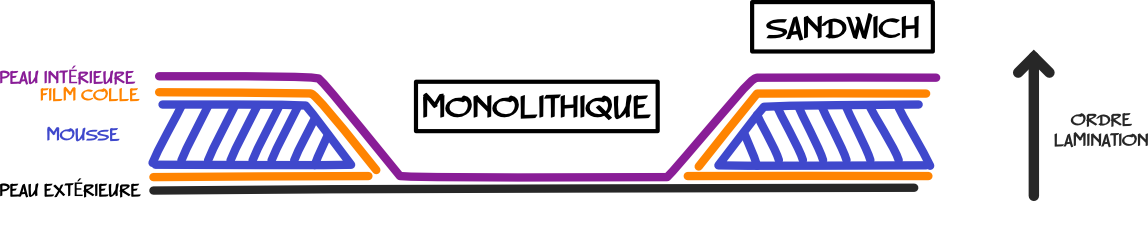
Après un dernier passage au four (autoclave), la pièce est (enfin) terminée ! Vient alors le temps du contrôle. Pour s’assurer qu’elle ne présente pas de défauts particuliers, un contrôle non-destructif (NDT) est réalisé. Des ultrasons sont envoyés au travers du composite, permettant d’avoir des informations sur la structure de la pièce. Il s’agit en quelque sorte d’une échographie.
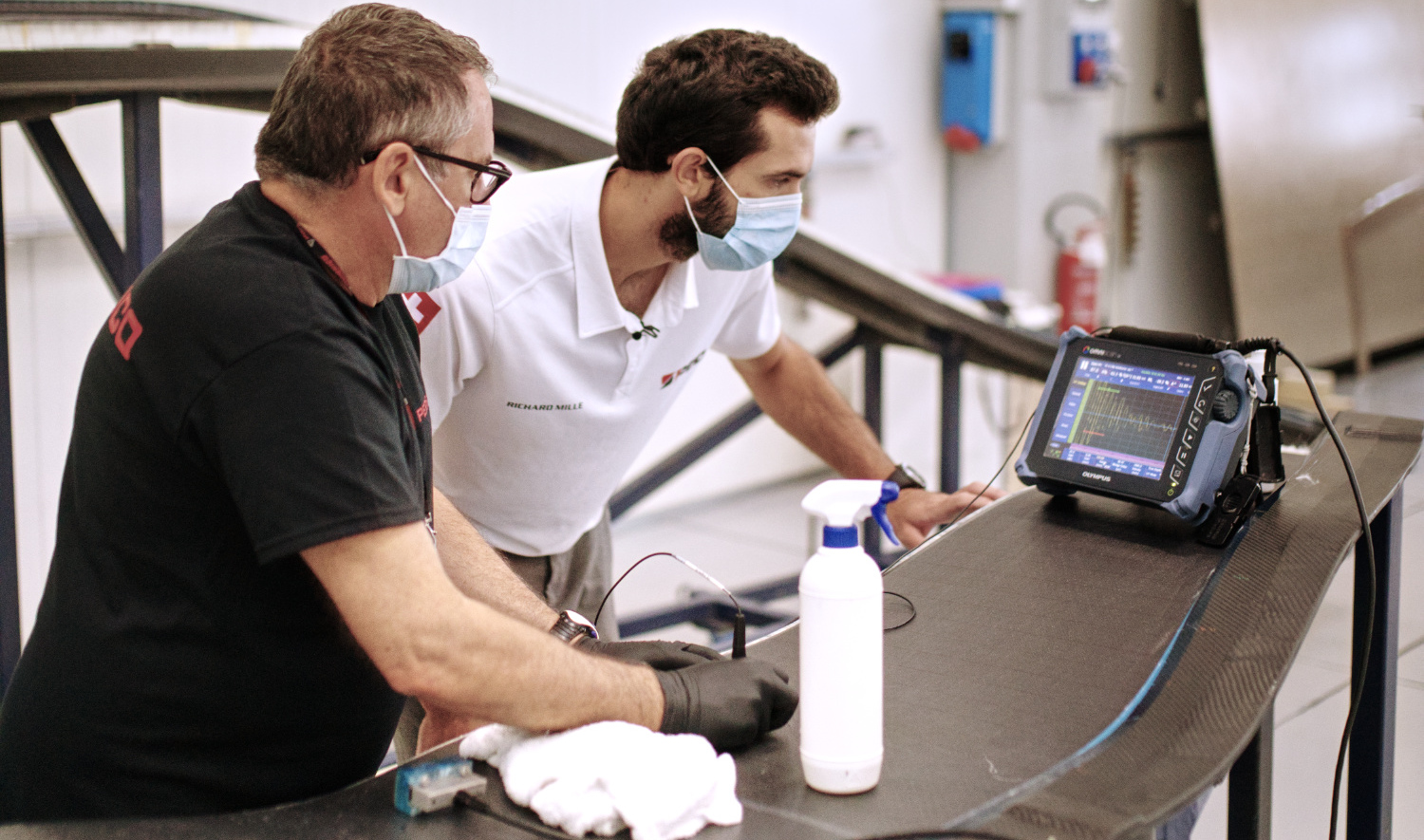
Benoît participe au contrôle non-destructif sur le chantier naval.
Les mousses sont maintenues en place sur le carbone grâce à un film de colle. Le tout repart alors en cuisson pour que le film de colle durcisse et fige complètement le positionnement. Puis le chantier continue la lamination en déposant les plis de la peau intérieure de la pièce. Le schéma suivant reprend la séquence complète de la lamination :
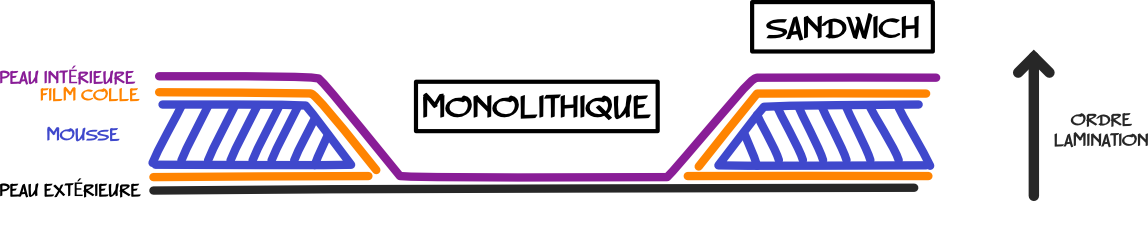
Après un dernier passage au four (autoclave), la pièce est (enfin) terminée ! Vient alors le temps du contrôle. Pour s’assurer qu’elle ne présente pas de défauts particuliers, un contrôle non-destructif (NDT) est réalisé. Des ultrasons sont envoyés au travers du composite, permettant d’avoir des informations sur la structure de la pièce. Il s’agit en quelque sorte d’une échographie.
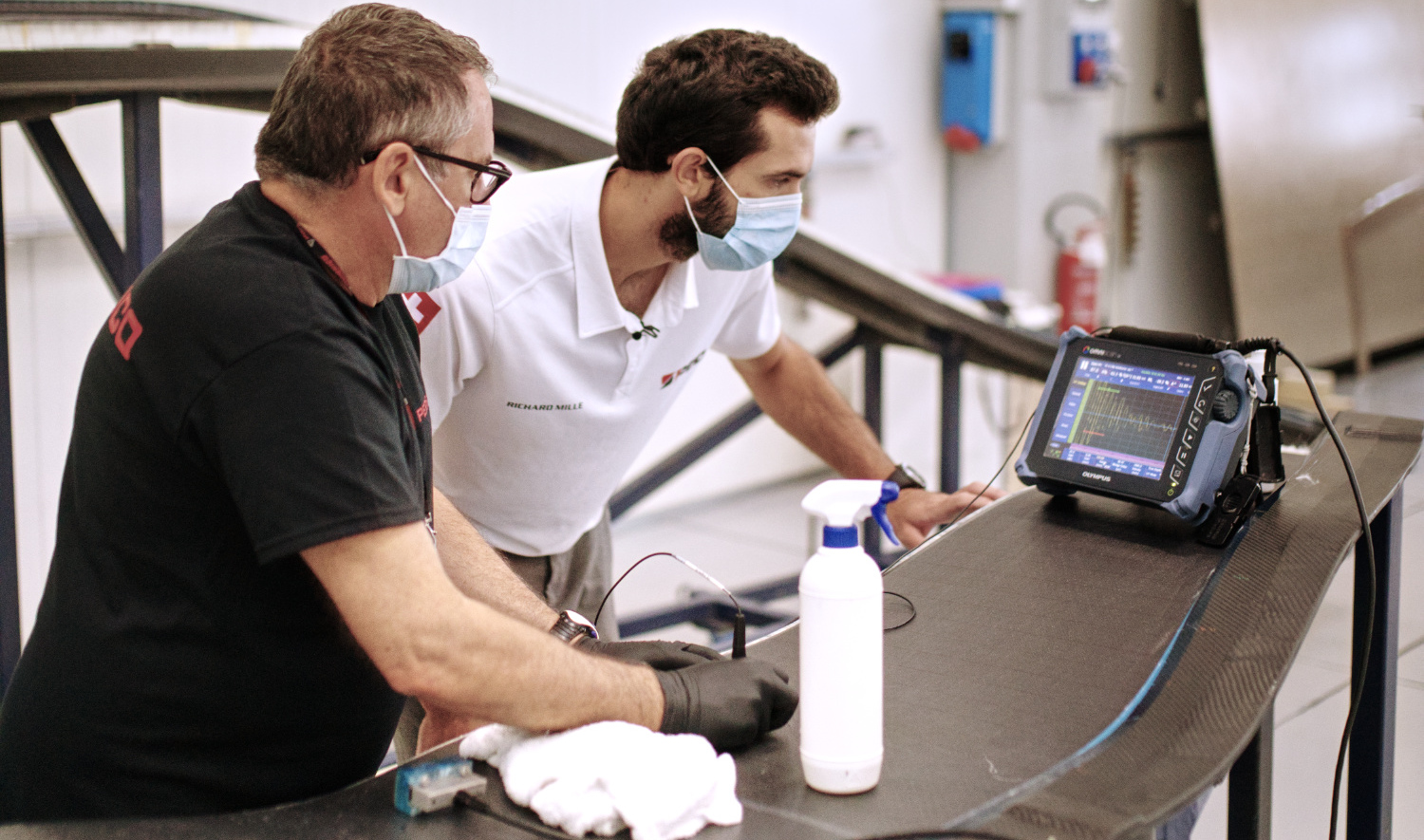
Benoît participe au contrôle non-destructif sur le chantier naval.
Vous voulez en savoir plus ?
Plongez-vous dans la construction en vidéo !
Et Ensuite ?
Une fois que la qualité de la pièce est assurée, Persico Marine réalise un scan 3D, permettant d’obtenir la géométrie exacte de la pièce produite. Ce scan est essentiel pour la suite des opérations: l’assemblage des différentes pièces entre elles !
Copyright 2024 | SP80 | Tous Droits Réservés